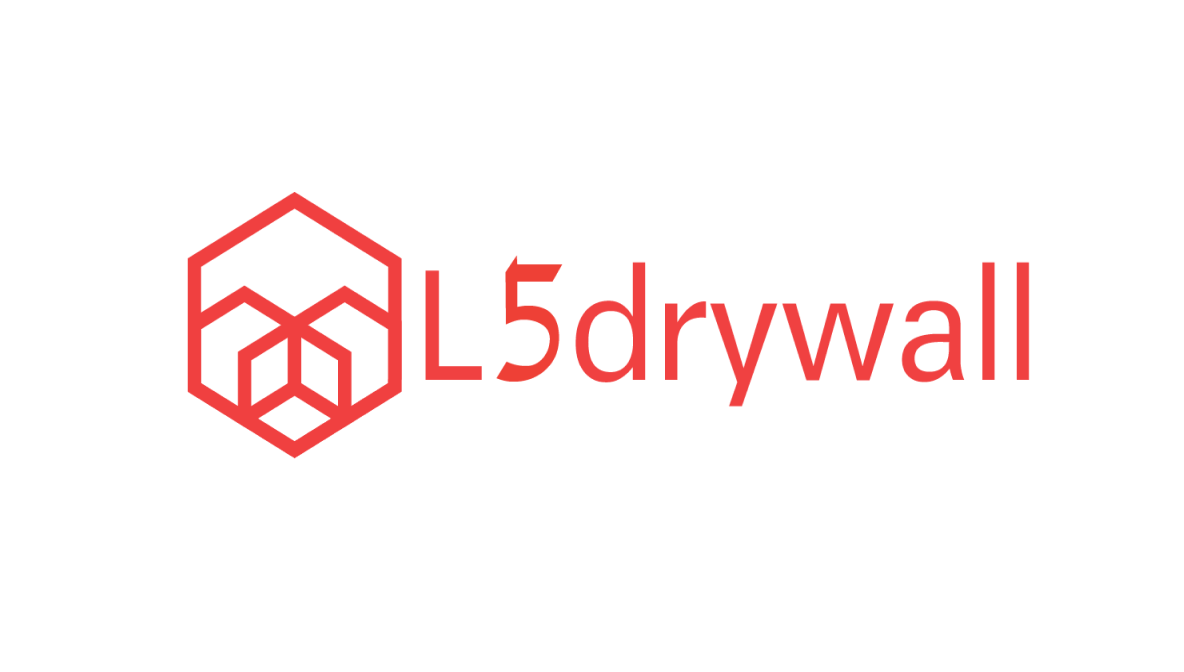
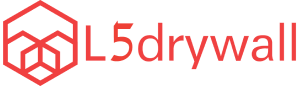
L5 Drywall, Inc., established in 2014, is a premier drywall installation company serving the San Francisco Bay Area.
Founded by industry veterans with over 30 years of combined contracting experience, the company specializes in delivering high-quality drywall services to general contractors in San Francisco, San Jose, and surrounding regions.
With a robust workforce capable of managing projects of any scale, L5 Drywall combines extensive expertise and high-energy commitment to meet diverse drywall installation challenges.
The Challenge
Level 5 Drywall, a premier drywall installation company, faced a familiar challenge that many construction companies have grappled with. Two years into their existence, their productivity levels were going down. Investigations revealed that while the workday ended on time, the work remained incomplete.
Problems with Manual Time Tracking
Level 5 Drywall had been following the traditional methods of manual time card process where every employee submitted their time sheets at the end of the work week. The time sheets were perfect, capturing eight hours of work by logging in at the appointed time and logging off after eight working hours, but the work site told a different story altogether.
Projects were getting delayed, and inflated labor costs hinted that the hours reported didn’t really match with hours worked. The management realized that they needed a more reliable time tracking program as the manual time card process was outdated and needed an overhaul.
The Solution
To tackle the drop in productivity and to boost efficiency, Level 5 Drywall decided to adopt modern timecard apps for their workforce. They needed an application that would provide real-time precise data on employee attendance and hours worked to ensure accurate wages for their employees.
After experimenting with different time tracking solutions, they finally implemented Lumber Time Tracking.
The Results
Implementing Lumber Time Tracking - an application purpose-built for the construction industry proved to be a game changer for Level 5 Drywall. After implementing Lumber Time Tracking, they experienced -
- 25% increase in project productivity
- 8-12% reduction in labor costs
- Virtually eliminated time reporting disputes
- Streamlined workforce accountability
Revolutionizing Construction Time Tracking: The Level 5 Drywall Success Story
Two years into operation, Level 5 Drywall confronted a common productivity dilemma in construction: projects routinely overshot timelines despite finishing workdays on schedule and skyrocketing labor costs. The culprit was an outdated manual time card process.
Tracking work hours using traditional time cards is largely based on trust where employees logged 40-hour weeks without scrutiny. Project delays and increased labor expenses suggested discrepancies between reported and actual hours worked.
A surprise Friday site visit by the management uncovered reality: the worksite was empty, and workers were unreachable. Management realized the necessity to completely revamp their antiquated time tracking system.
During the unexpected visit, it became obvious employees often left hours early. When questioned, they cited reasons like traffic or personal errands but still reported full eight-hour days. This gap between reality and records drained resources, delayed projects, and undermined accountability.
The Search for Change
Seeking efficiency, leadership turned to technological solutions for real-time and precise attendance tracking. Initial trials with various systems met resistance; employees criticized these apps as unreliable, generating concerns over pay accuracy due to poor site reception.
Challenges in Transition
Implementing new tech spurred a backlash. Workers missed the predictability of paper timecards, fearing lost flexibility and newfound accountability made manipulating hours impossible, but the leaders remained firm in fostering transparency and fairness.
Implementing Lumber Time Tracking for Efficiency
Key Lumber Features that Benefited Level 5 Drywall:
- Geofencing: Alerts for clocking in/out when entering or leaving job sites, ensuring precise time entries.
- Facial Recognition: Eliminates "buddy punching," preventing false time reporting.
- Smart Scheduling: Restricts clock-ins to scheduled times, curtailing unauthorized starts or overtime.
- Employee-Controlled Updates: Allows workers to update missing entries, emphasizing personal responsibility for accuracy and accountability.
- Labor Law Compliance: Enforces mandated breaks, like California’s 30-minute lunch rule, ensuring legal adherence.
While transitioning from manual to digital tracking posed challenges, the outcome was evident:
- Productivity Surged: Increased by 25% in some projects, with employee accountability spurring job completion focus.
- Efficiency Enhanced: Project hours decreased by 8–12%, cutting labor costs.
- Transparency Established: Disputes over hours practically vanished, with the app offering undeniable attendance records.